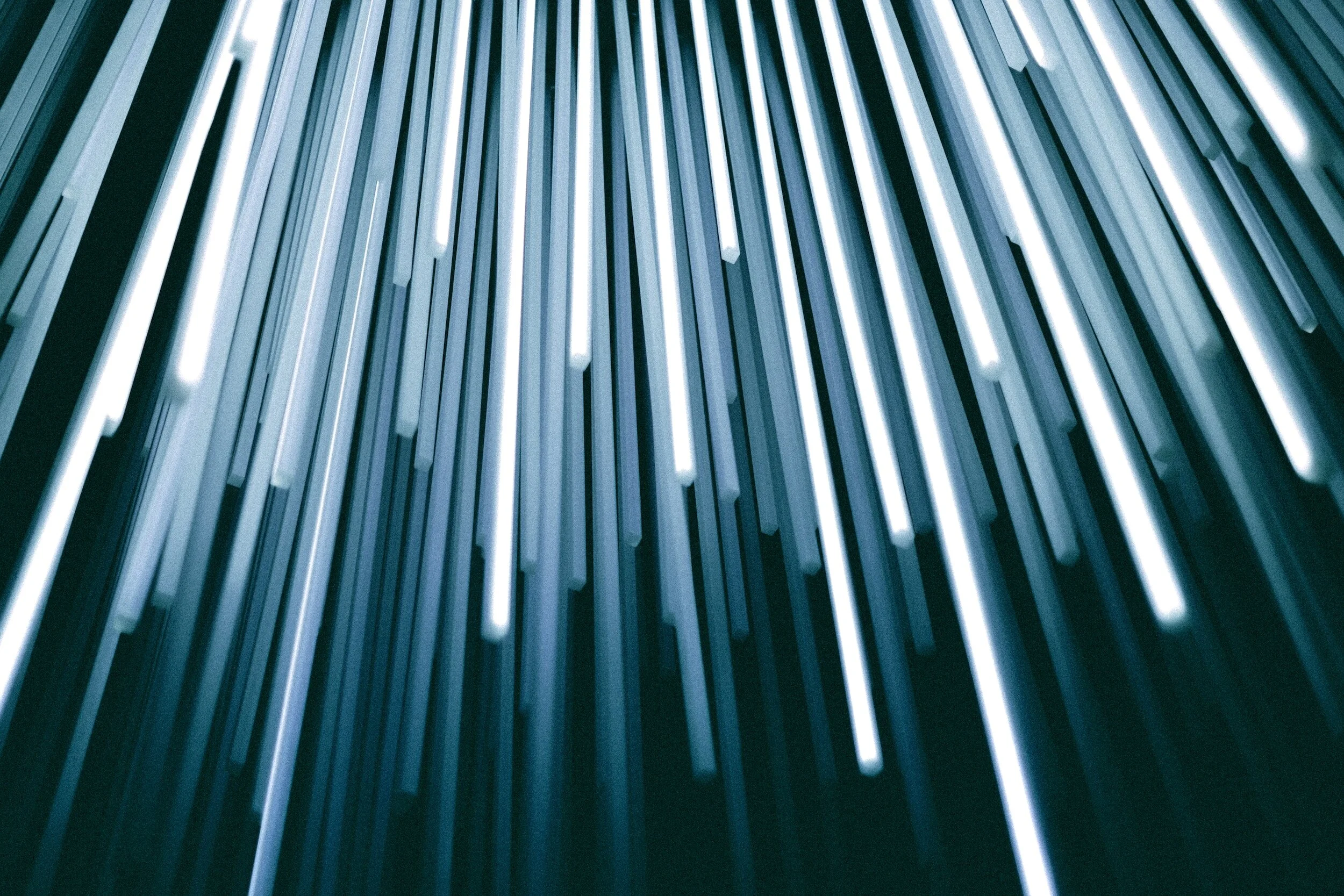
Products
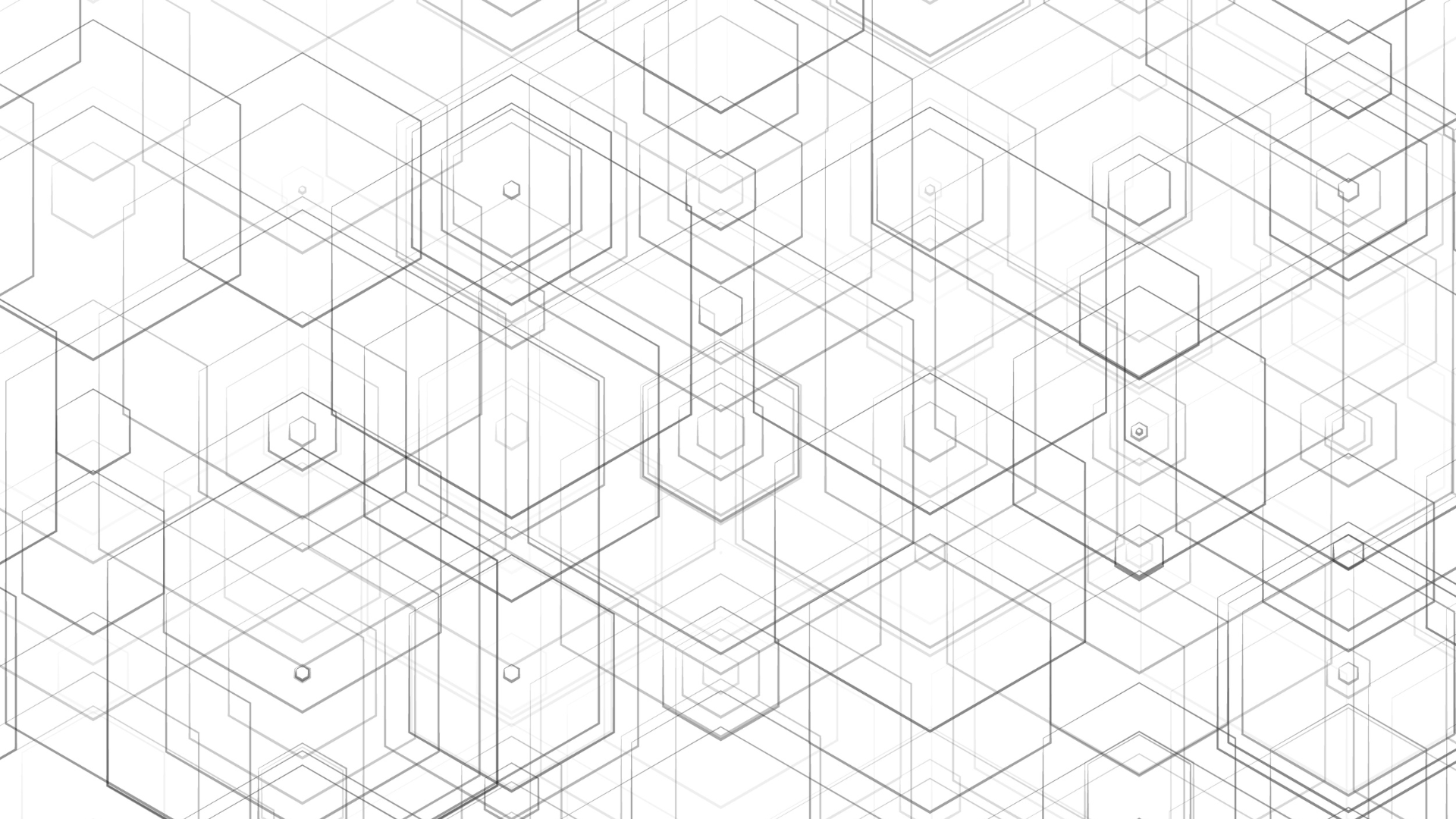
Vacuum furnaces
Vacuum furnaces are designed for degassing, brazing, annealing, hardening, melting, tempering, etc. in a vacuum or inert gas atmosphere.
A vacuum furnace may be needed, for example, for removing material stresses after forming processes, cleaning the surface of components (degassing), capillary brazing, hardening, etc.
The produced devices, which are characterized by high quality construction, are controlled manually or by an industrial computer with the possibility of archiving technological processing data. They are manufactured for use in low and high vacuum or inert gas atmospheres.
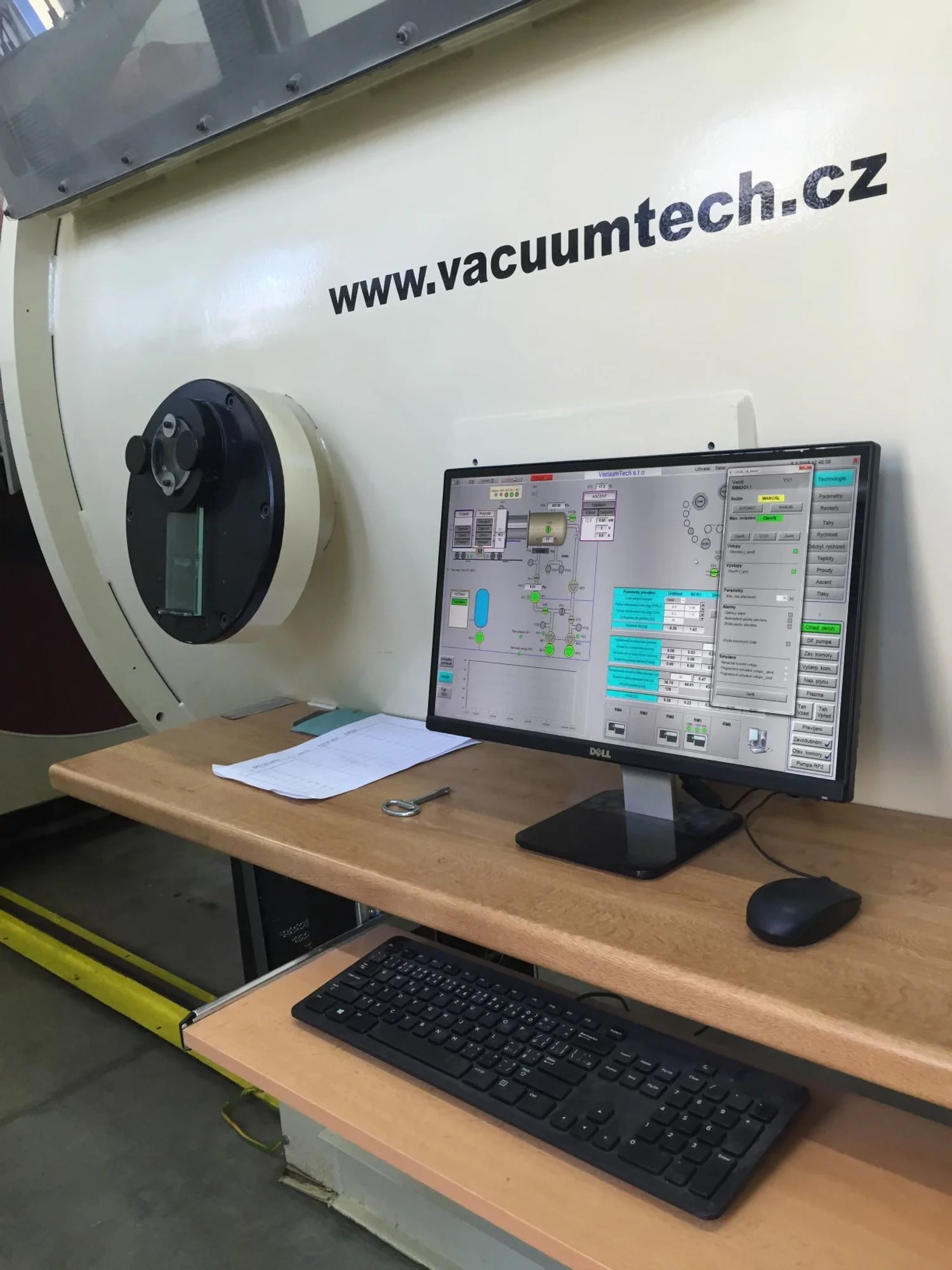
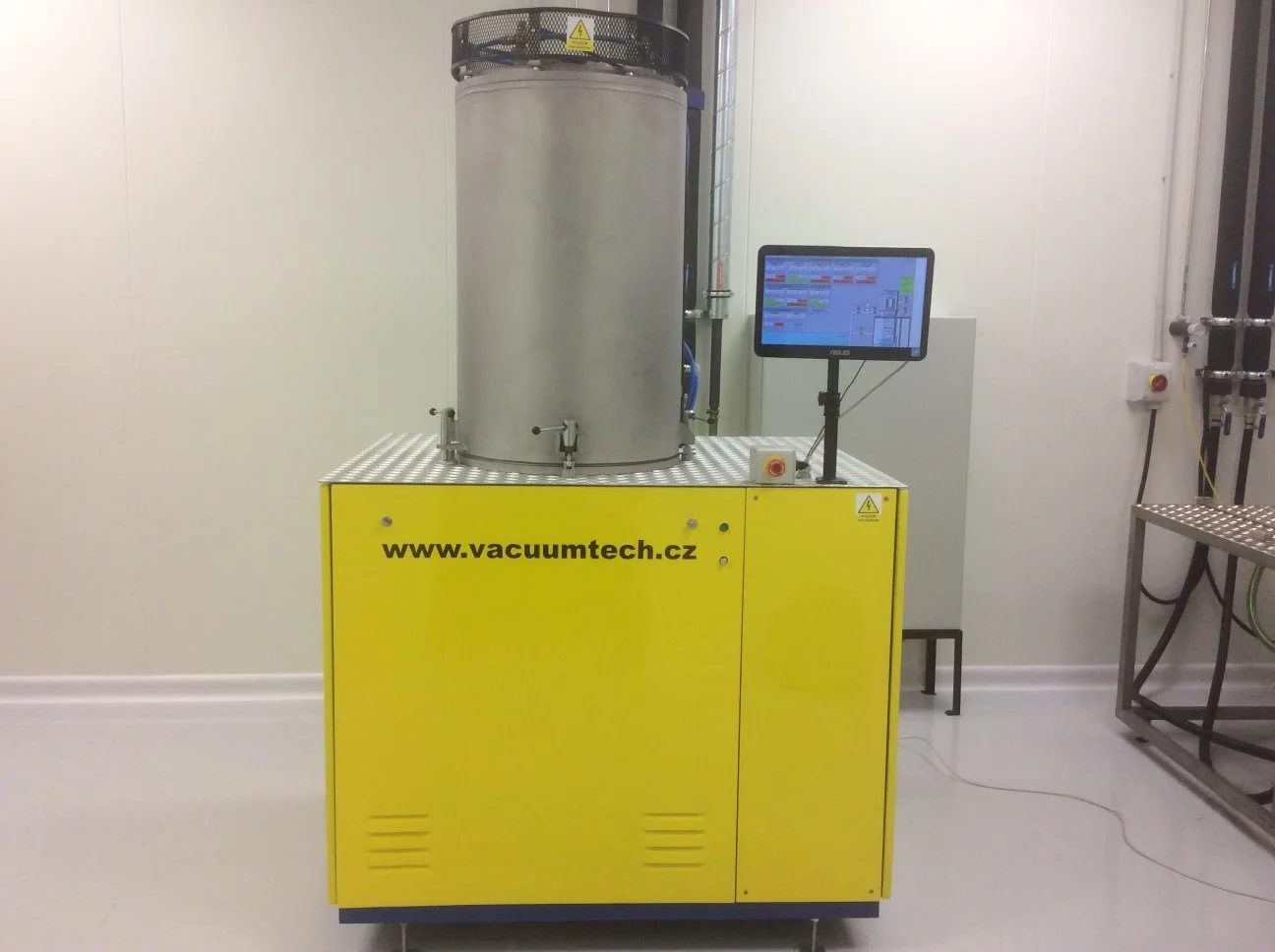

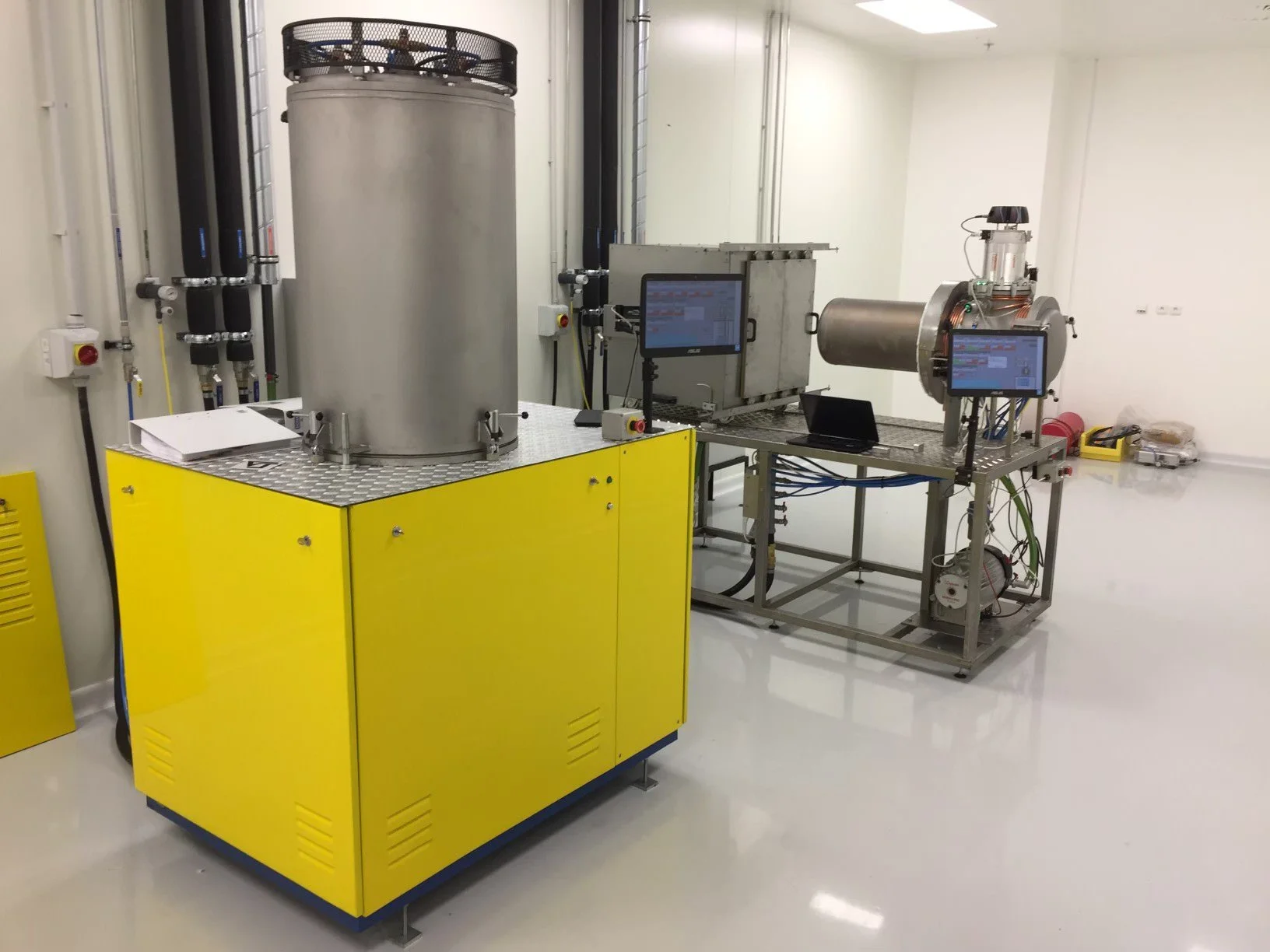
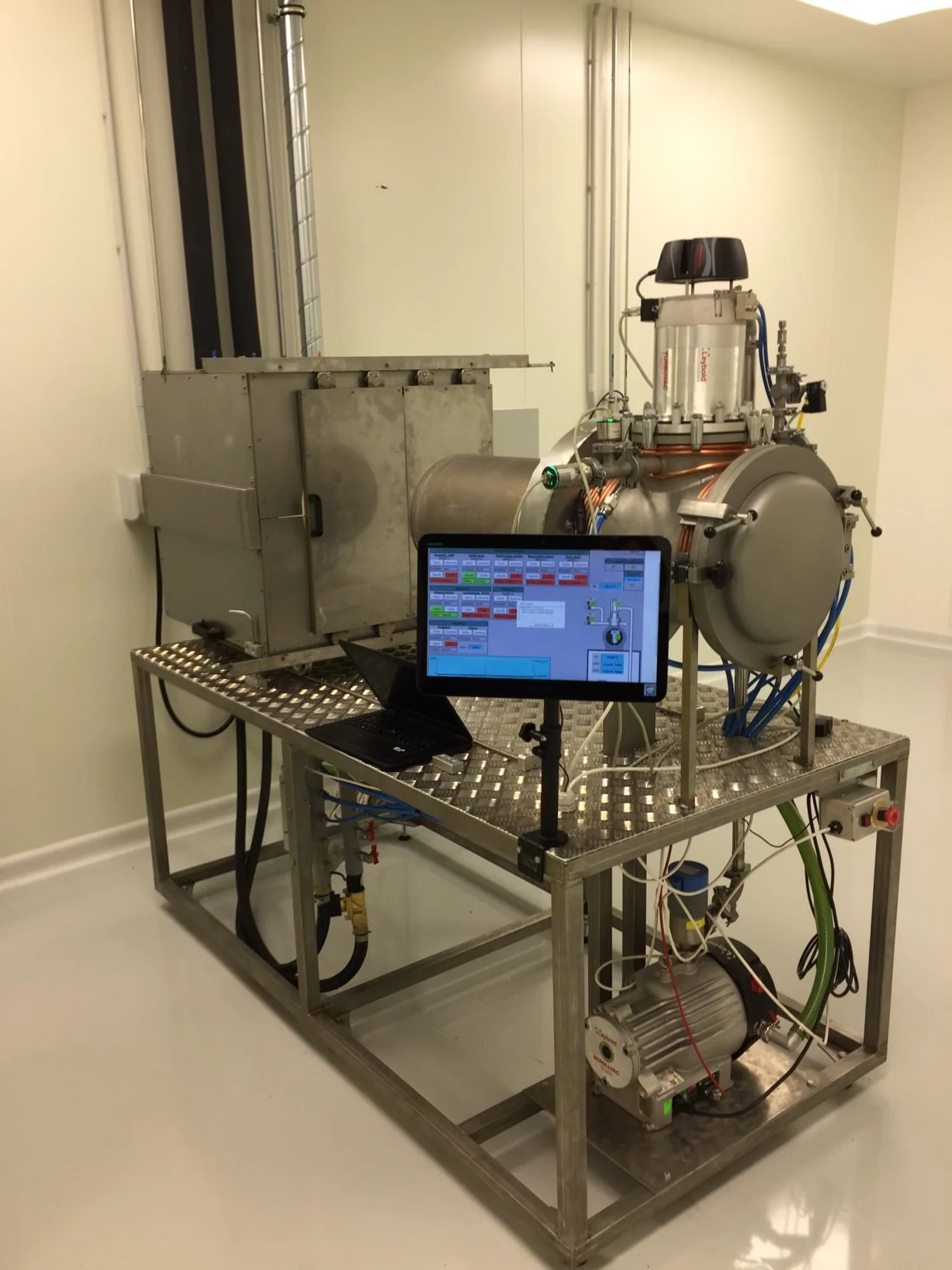
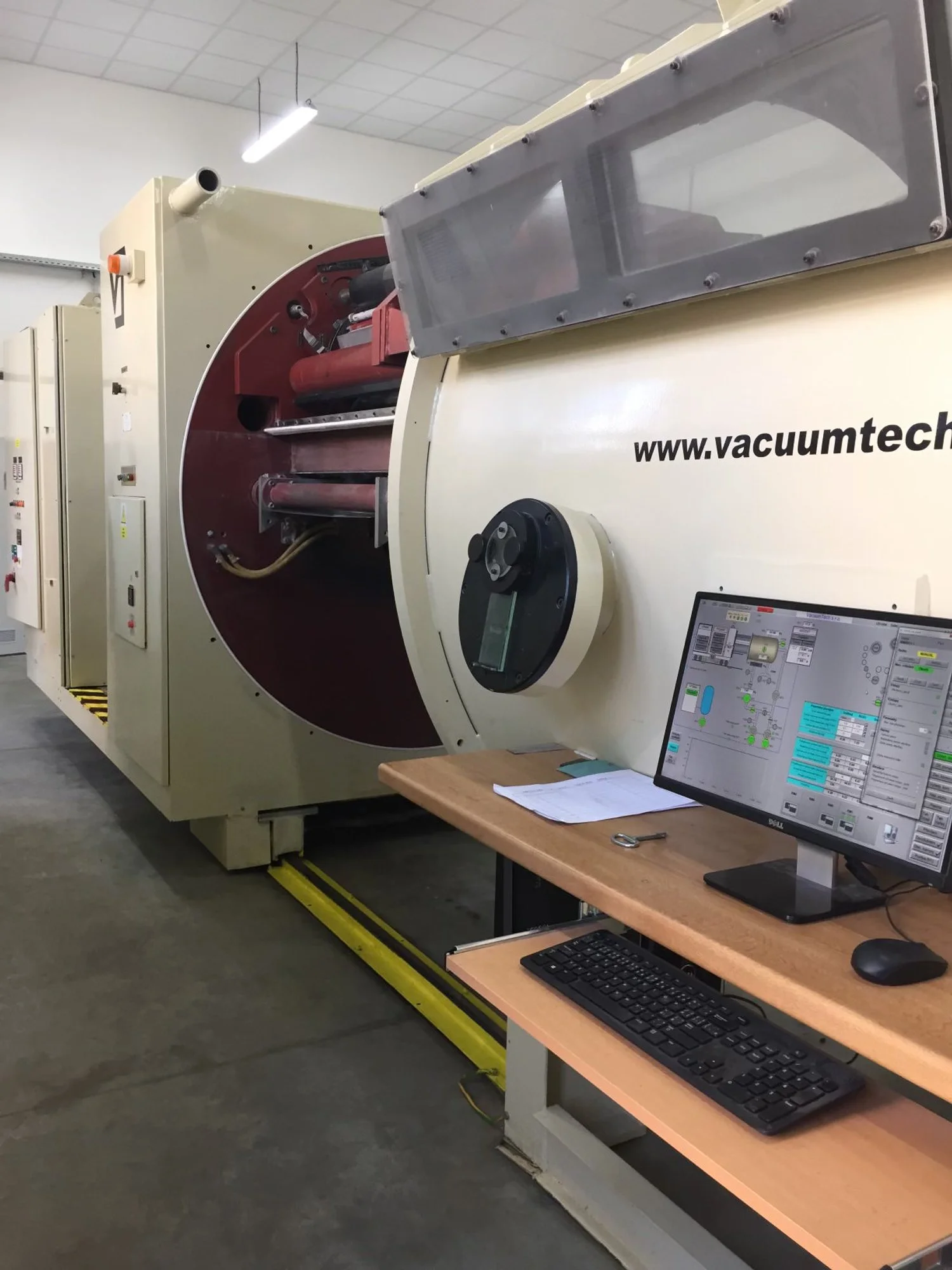
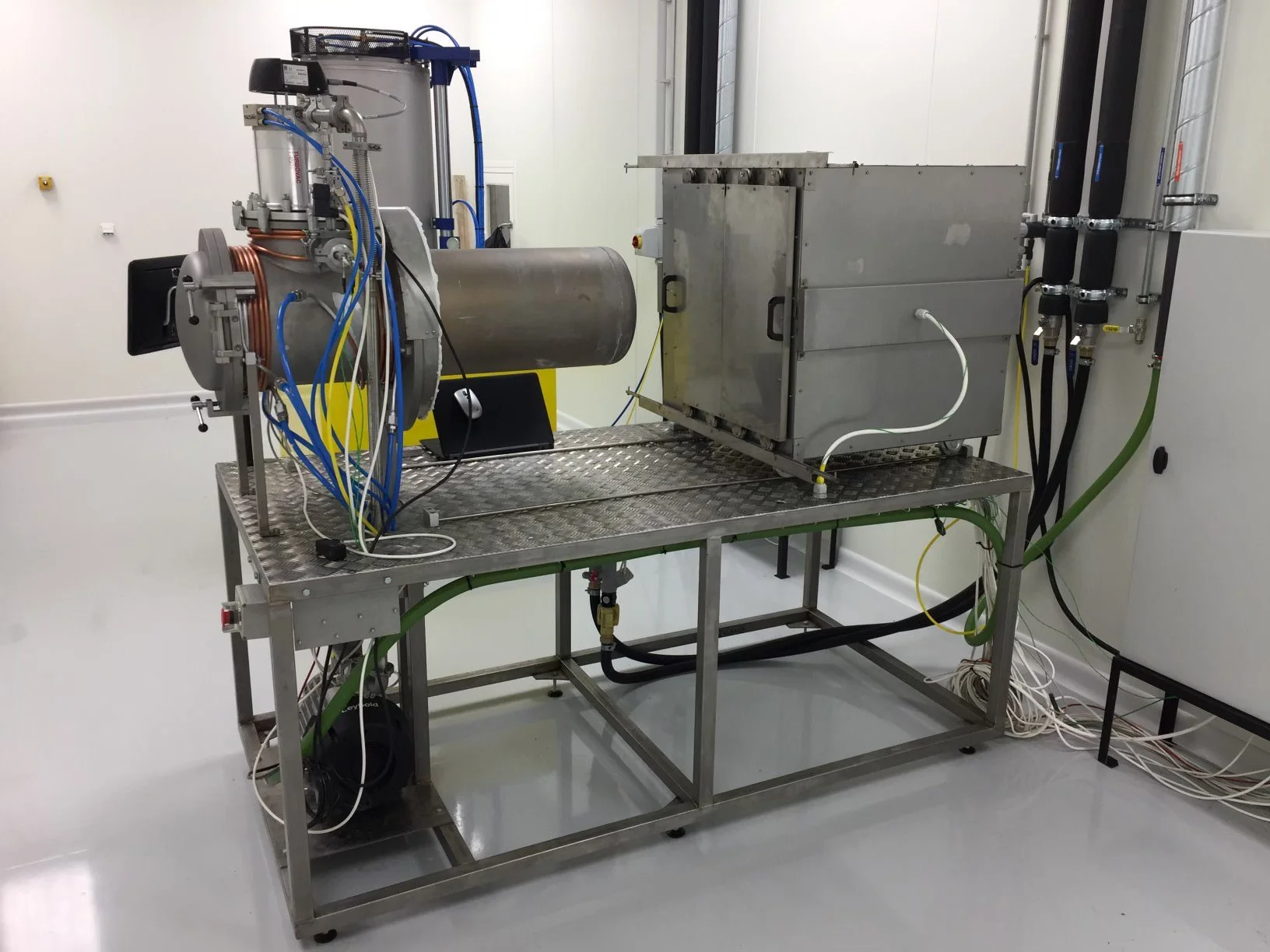
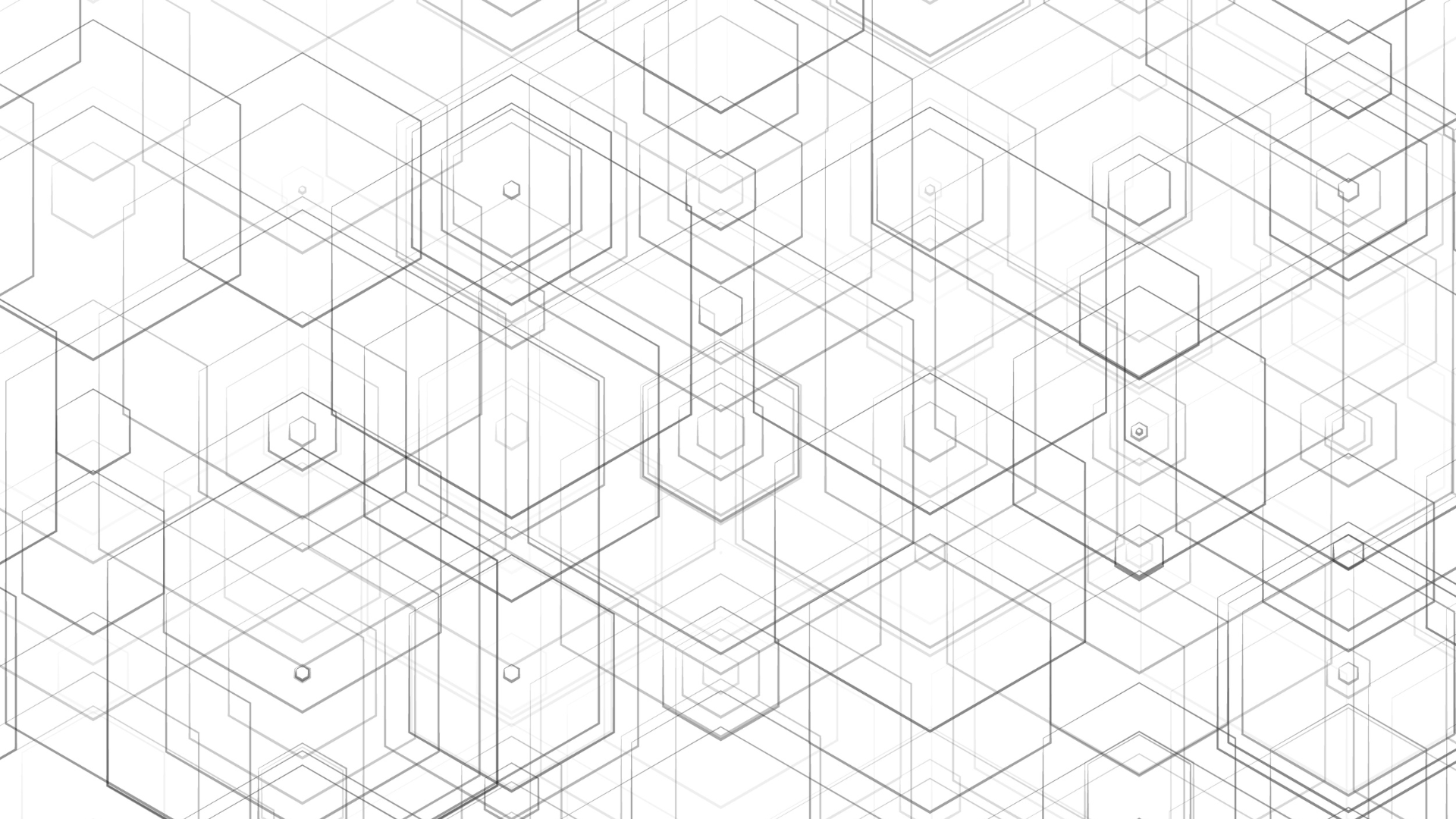
Steam coating vacuum equipment
It is primarily designed to apply thin layers of metals and non-metals to a wide range of materials.
The homogeneous solid layer is formed during the layer production by steaming the material at high temperature under high vacuum and its subsequent condensation on the substrate surface.
The steaming surface reflects the quality of the substrate. Pre-treatment is an integral part of the technology. Applications of this technology include optics, electronics, glass industry, food industry, etc.
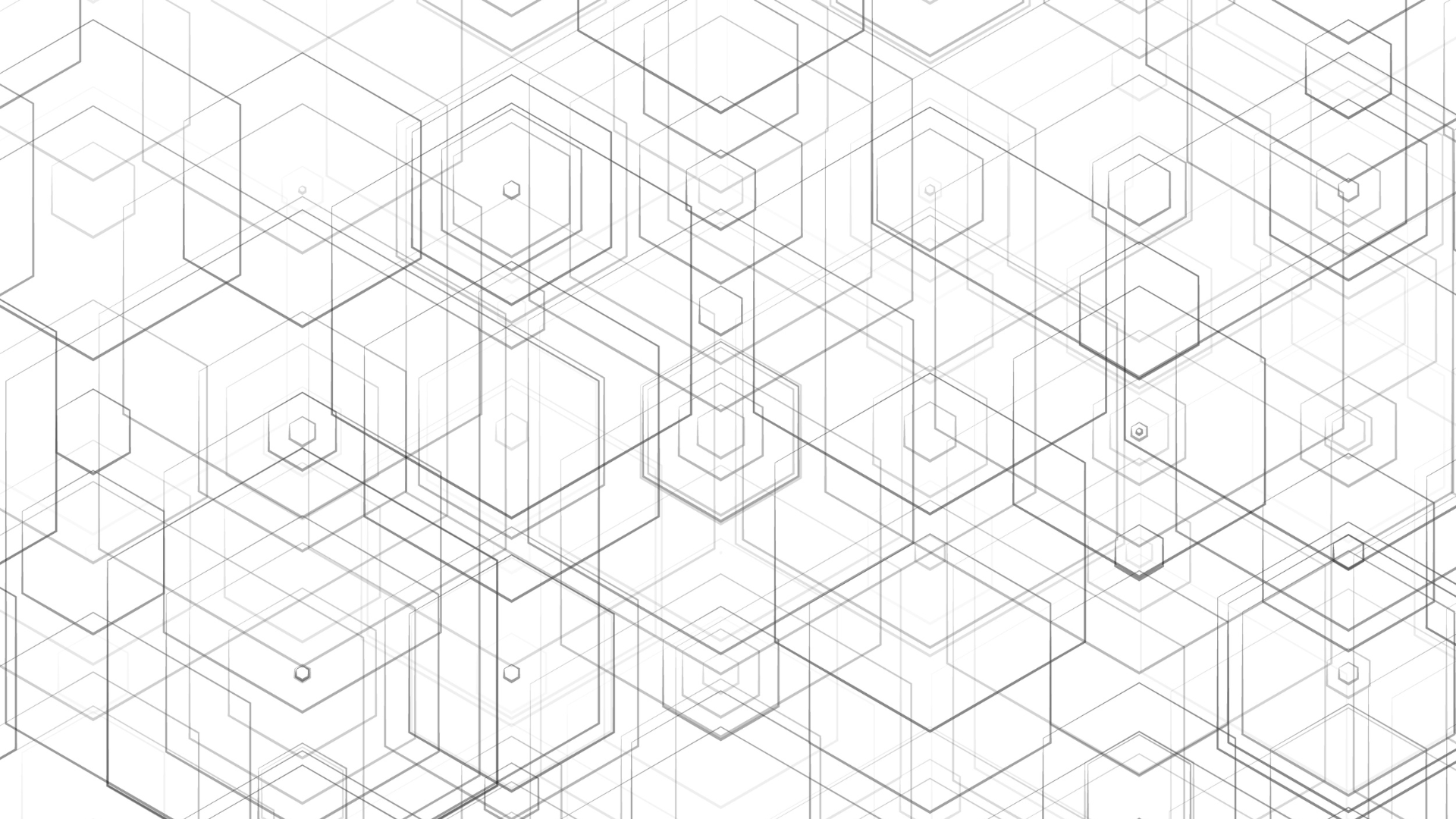
Vacuum sputtering equipment
Vacuum, also known as magnetron sputtering, is used for the application of thin metallic layers on metallic and non-metallic substrates. The principle is to deposit the layer in a plasma.The material to be deposited is removed from the target in a magnetron and bombarded with ions in a high vacuum while an inert or reactive gas is injected. After reaching a certain energy, the material molecules are directed towards the sputtering charge.
The advantage of this process is that, compared to sputtering, the target particles are transferred at a very low temperature so that no deformation of the substrate occurs.
The technology of these devices is used not only in the glass and automotive industries, optics, electronics, for decorative purposes, but also in engineering, for example in the application of hard coatings.


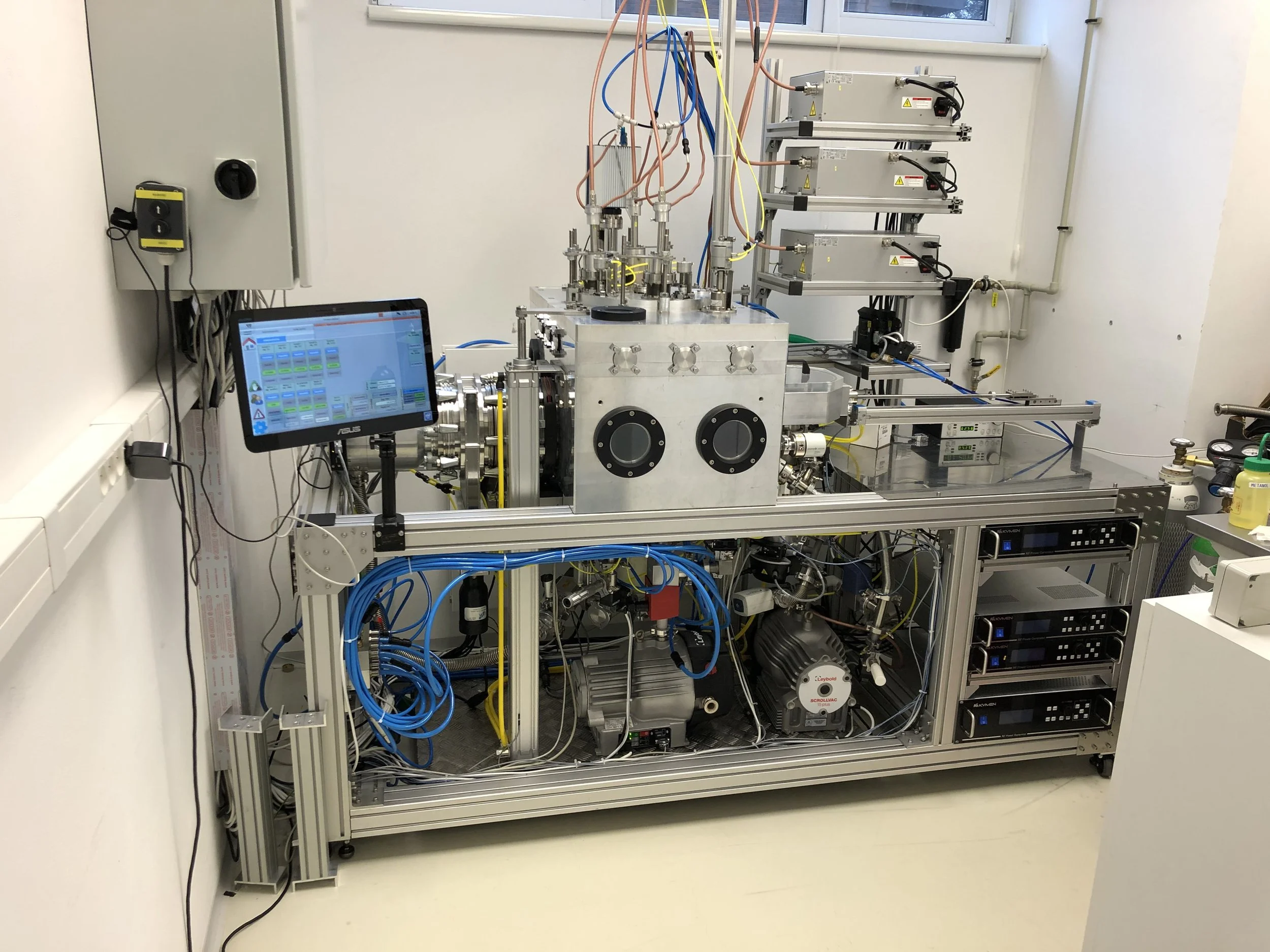
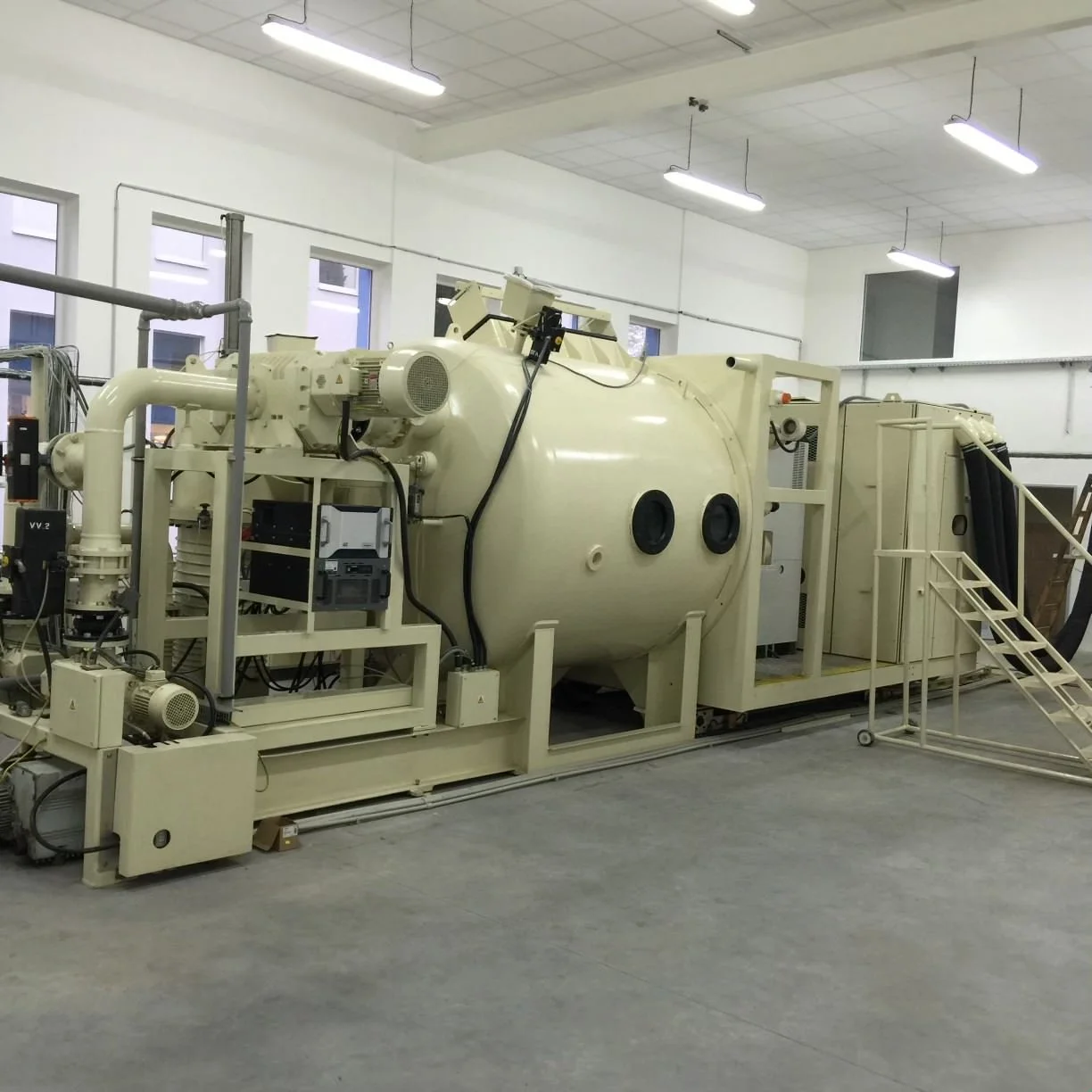
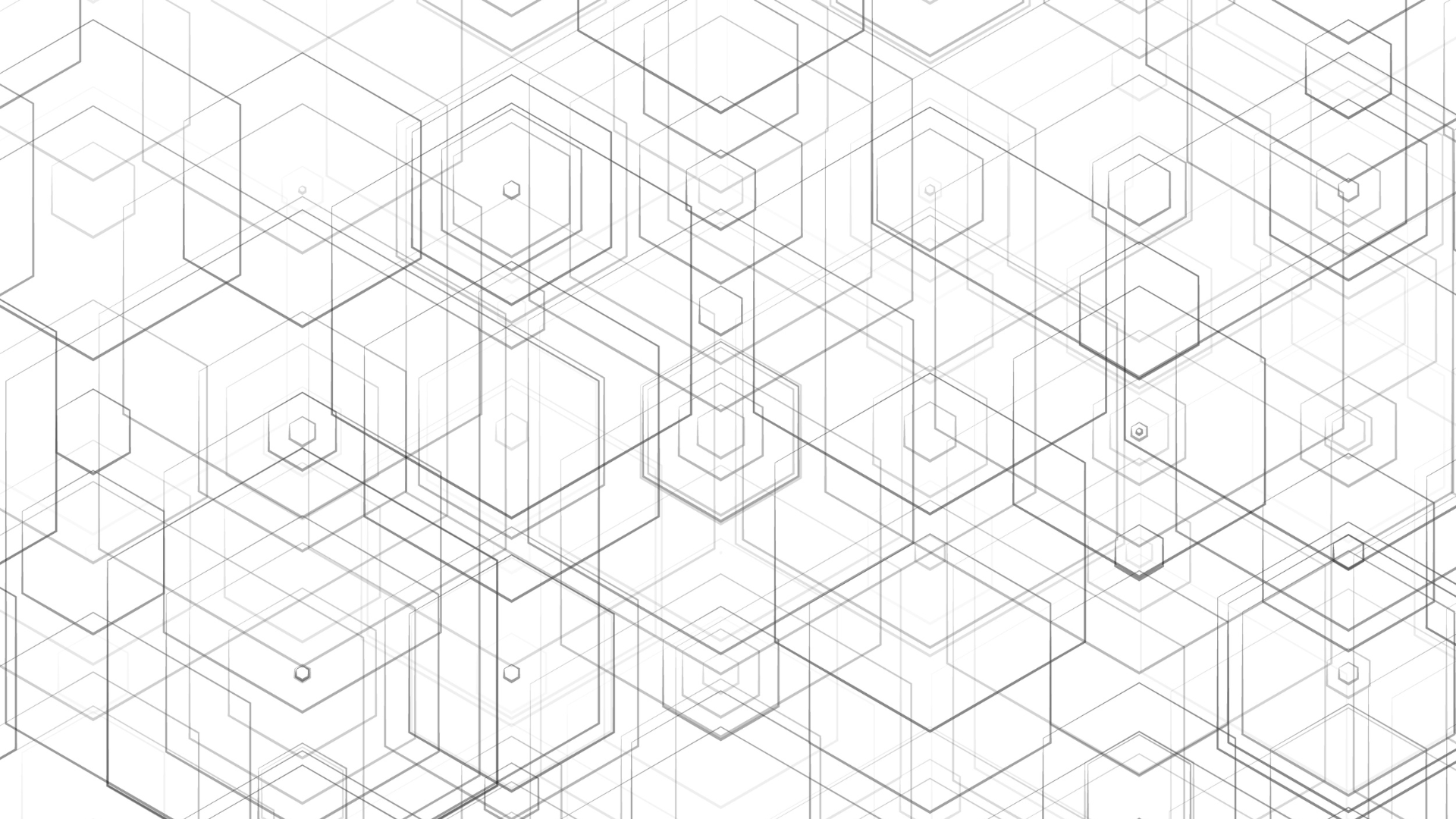
Hydrogen Furnaces
These furnaces are used for thermomechanical processes such as brazing, sintering and cleaning of metallic materials. They are mainly used in the engineering industry.
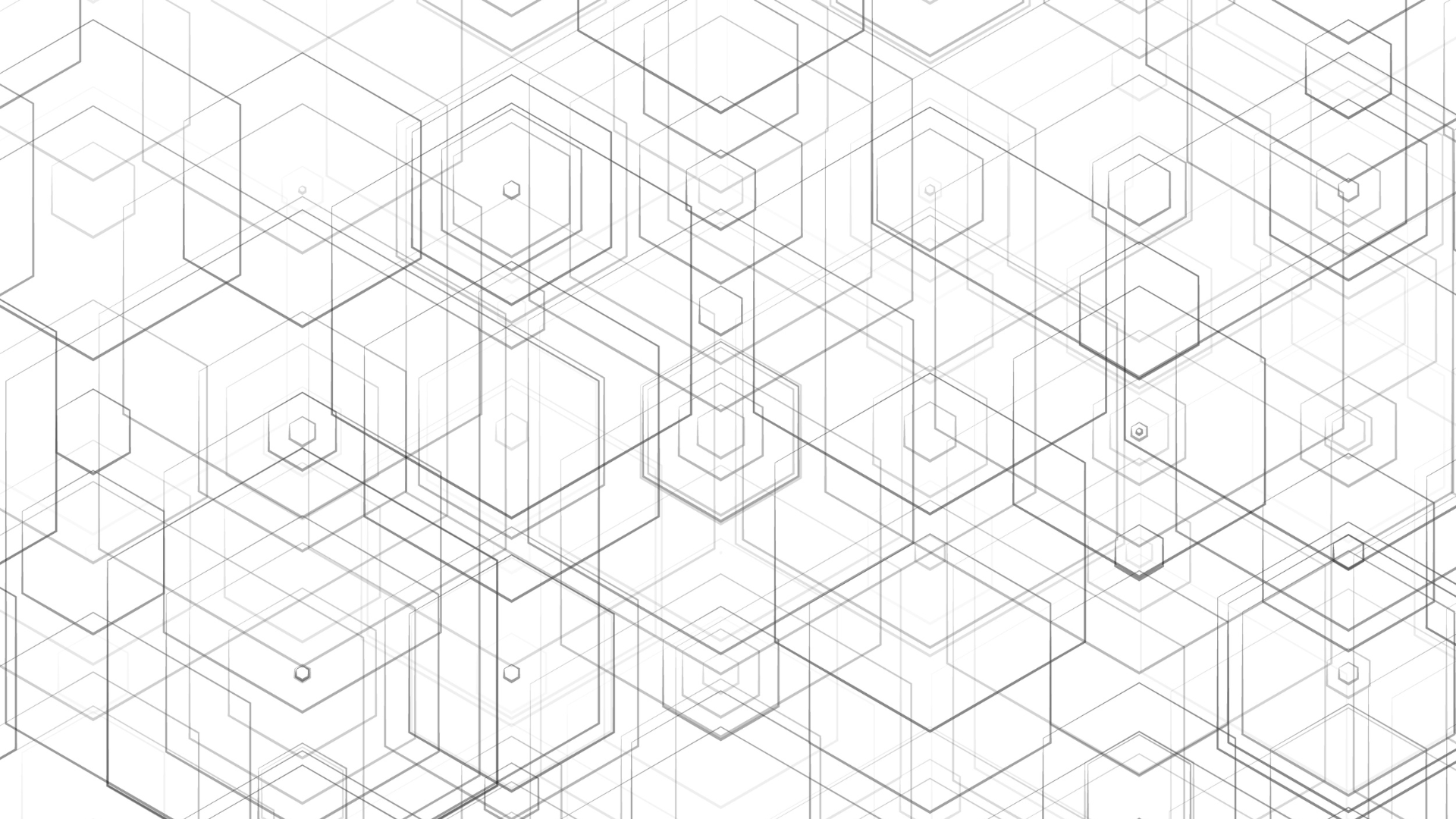
Plasma, Microwave and Ultrasound Equipment
Plasma, microwave and ultrasonic equipment are suitable for surface cleaning and surface stress removal. These technologies are very significantly applied prior to the application of coatings by sputtering and steaming technologies.
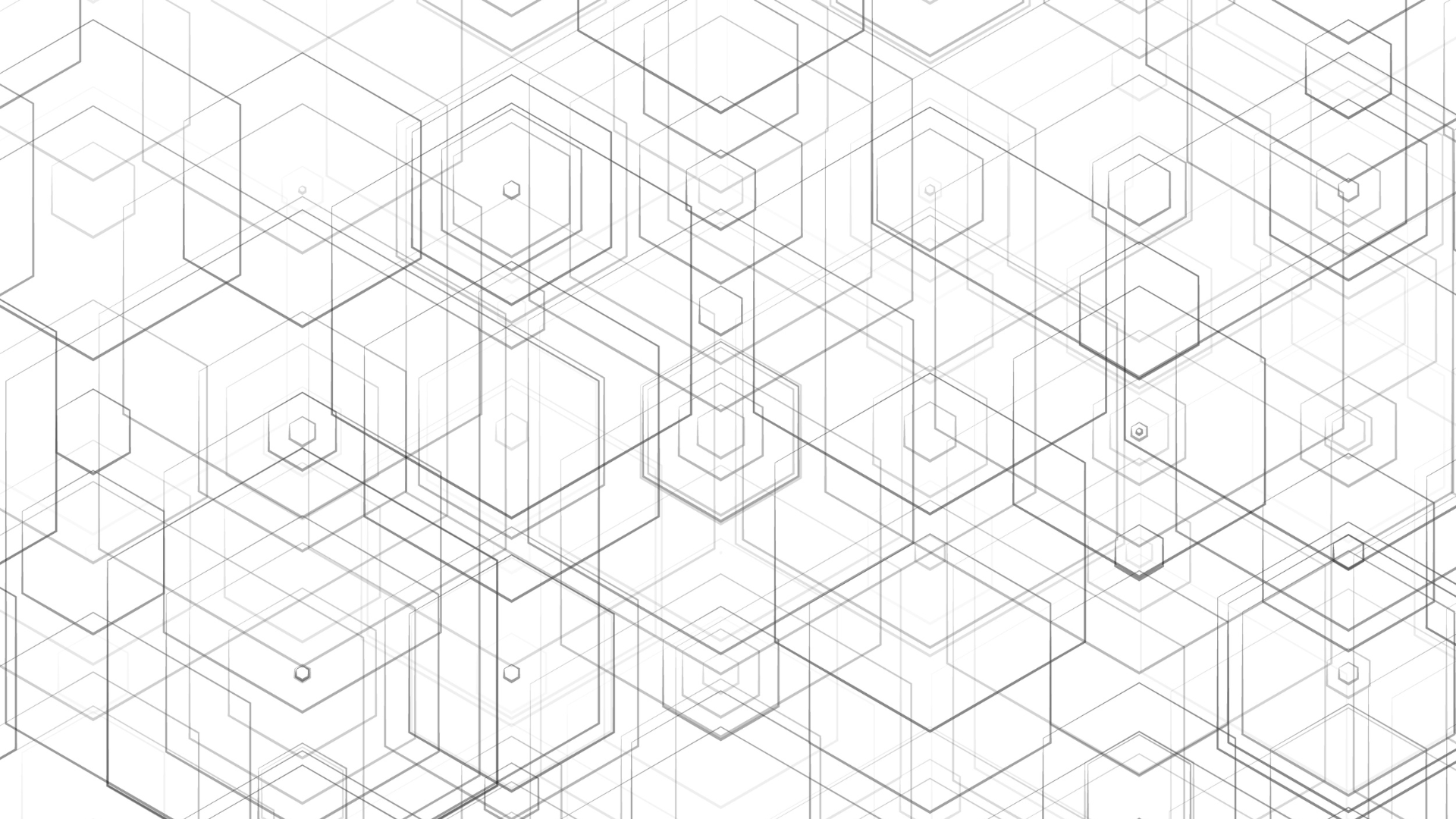
Vacuum Drying Furnaces
Vacuum drying ovens are used to dry various substrates in a vacuum. They are used in the chemical, food, automotive, engineering, electronics and pharmaceutical industries.
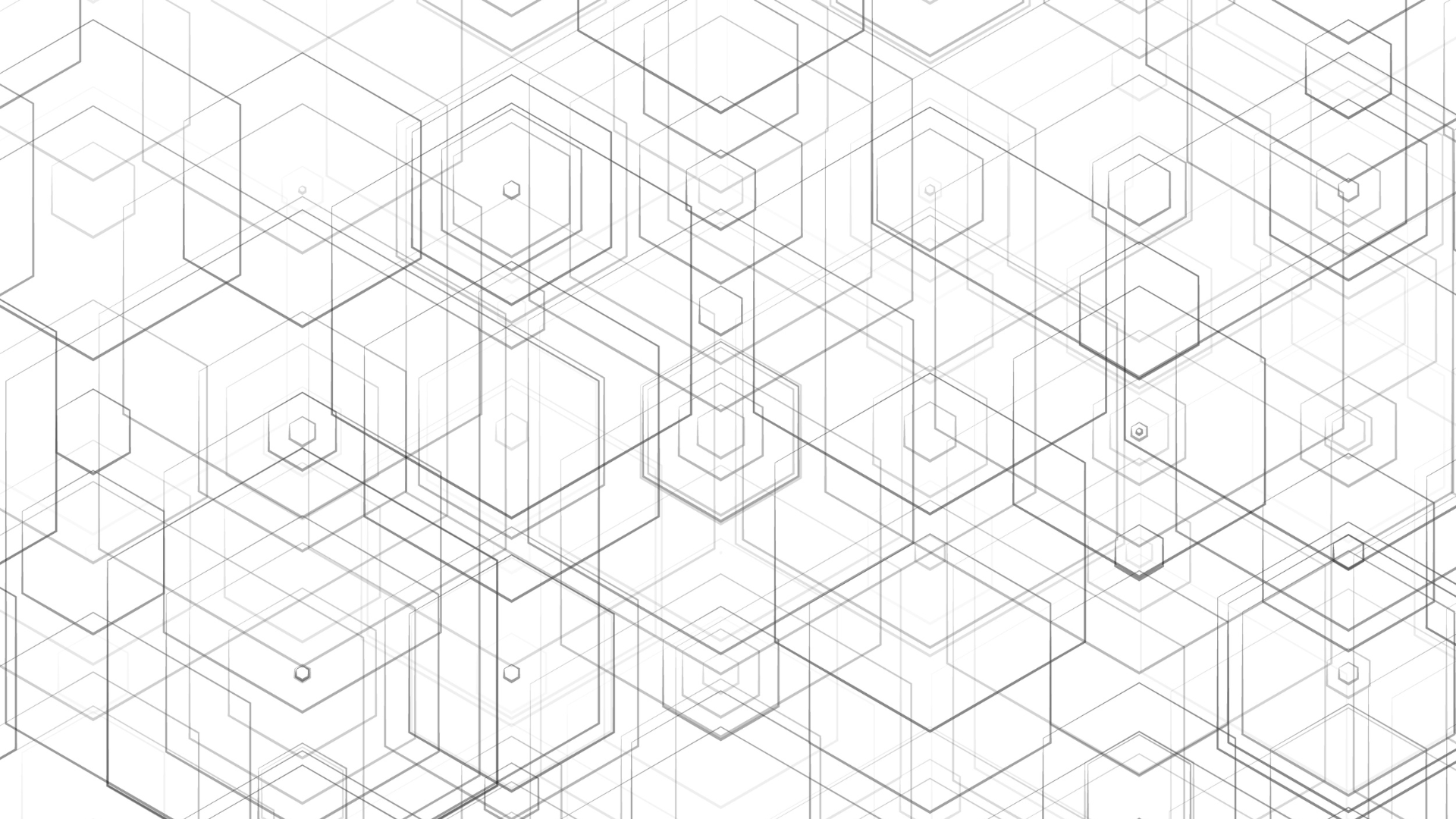
Plasma furnace with vertical crystallizer
Plasma heating equipment for the production of metal ingots with vertical crystallizer and atmosphere control.
The equipment is capable of producing and remelting pure metals, alloys of the type (Ni - Al, Ti - Ni, Ti - Al and various types of steel).
The resulting ingots represent compact material for further manufacturing processes, mechanical and heat treatment or various experimental operations.
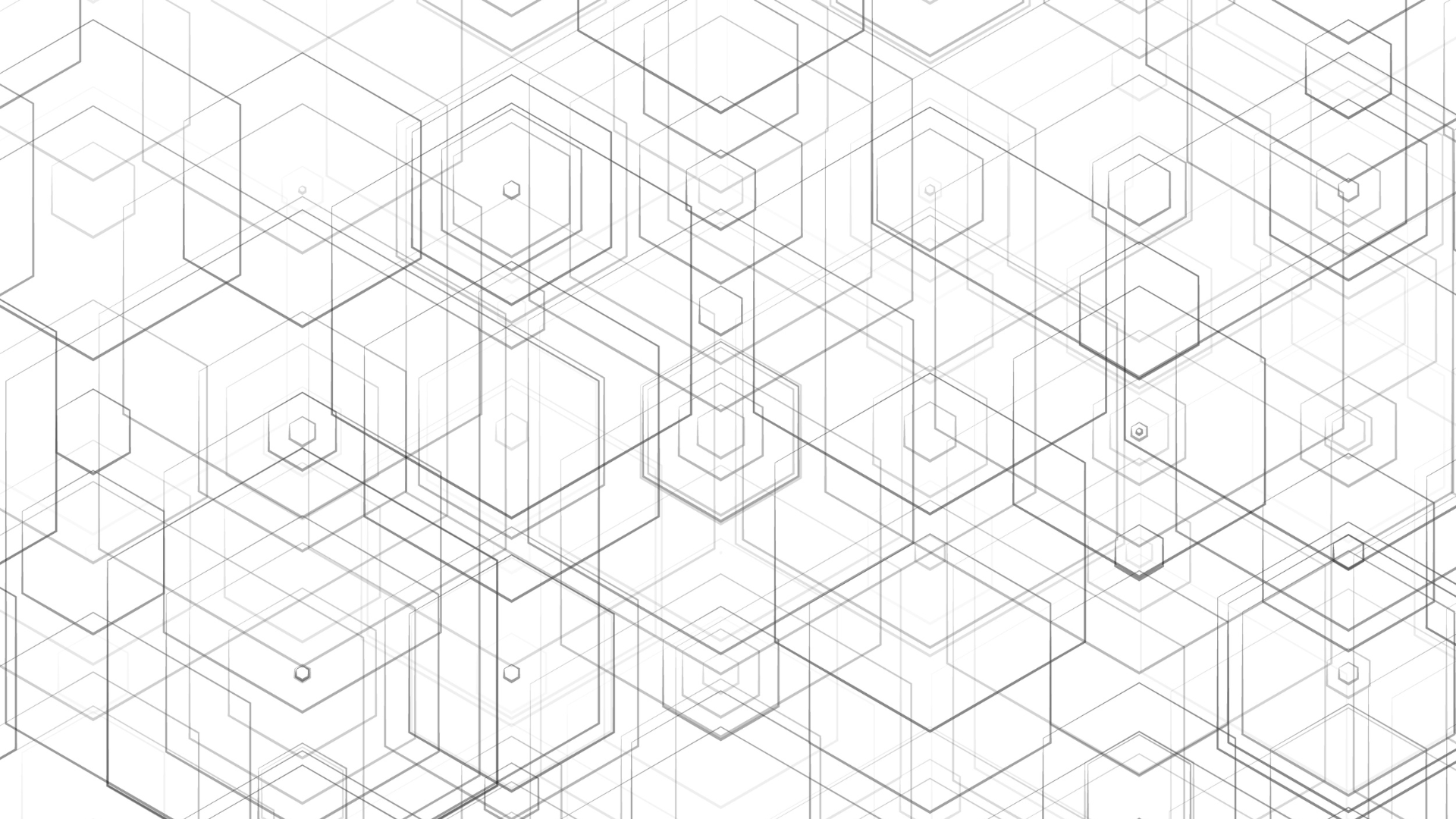
Czochralski's method of drawing single crystals
The principle of the method is that a germ crystal is immersed in the melt in a crucible, partially melted, and then pulled out of the melt at a slow speed. The temperature distribution across the cross-section of the crystal must be symmetrical with respect to the axis of the crystal, which is aided either by rotation of the germ or by rotation of the crucible with the melt, or both. The rotation of the crystal and melt ensures sufficient homogeneity of the melt and a minimum width of the diffusion layer at the crystallization front. The crucible with melt is placed in a closed furnace space under vacuum, nitrogen or inert atmosphere to prevent oxidation of the melt. Resistance or induction heating is used as heat sources.
Commonly used pulling speeds are in the range of 1-10-4 to 1-10-3 cm-s -1 with a rotation speed of 0.1 to 1 s-1 . The temperature of the melt in the crucible should be maintained at a prescribed value just above the melting point of the material with a relatively high accuracy of ±1 K. The isotherm corresponding to the crystallisation temperature of the substance lies above the surface of the melt. The temperature of the melt in the crucible increases downwards towards the bottom of the crucible. Both the single crystal nucleus and the growing crystal serve to efficiently dissipate heat away from the crystallization front. The shape of the melt surface is influenced by gravity and the surface tension of the melt. The crystal drawing speed, rotation rate and temperature of the melt in the crucible also affect the shape of the crystal-melt phase interface. At high melt temperatures or high drawing speeds, the solidification isotherm lies higher above the melt surface, thereby reducing the crystal diameter. Conversely, a decrease in melt temperature and drawing speed leads to an increase in crystal diameter, which is exploited technologically.
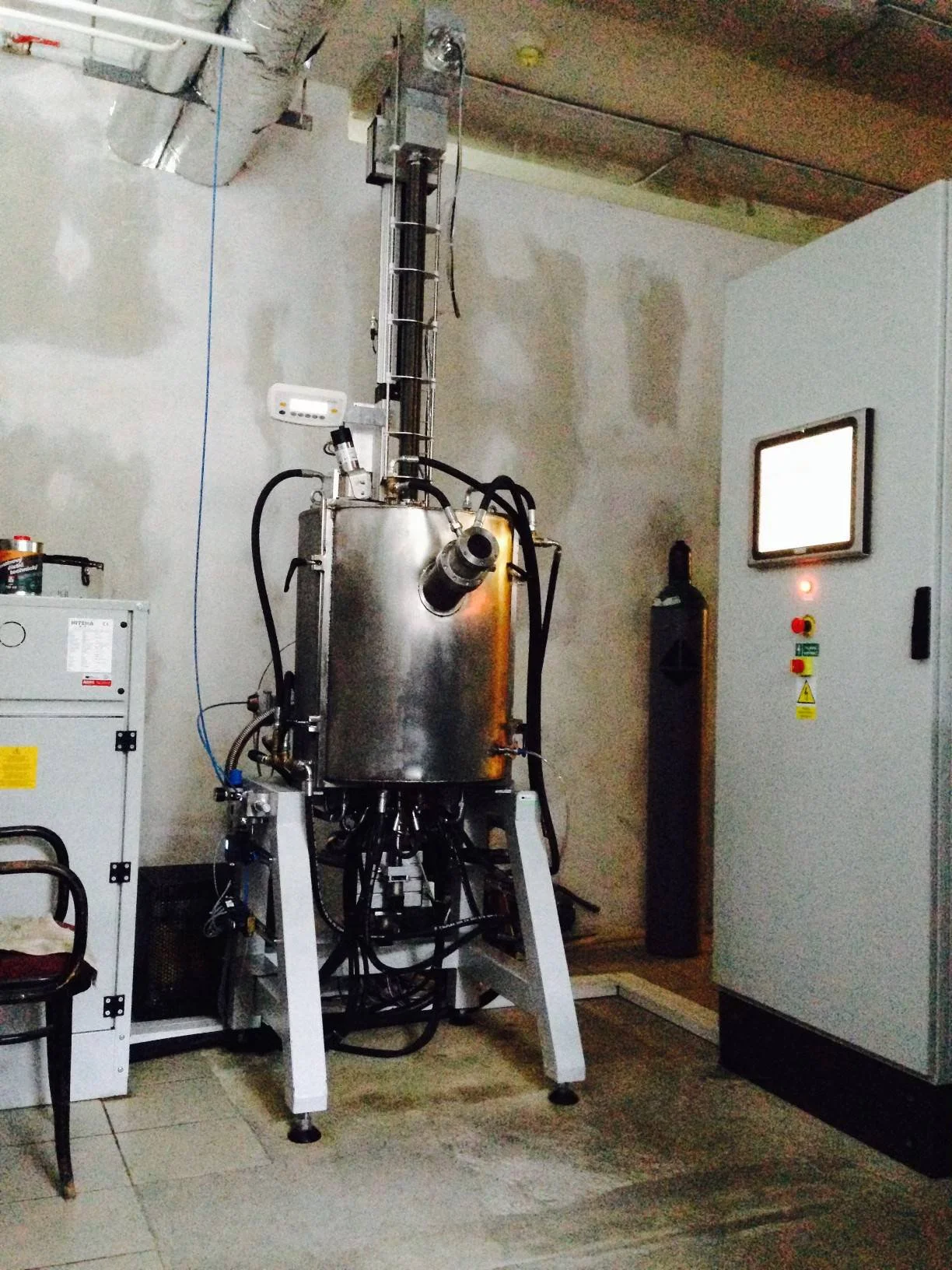
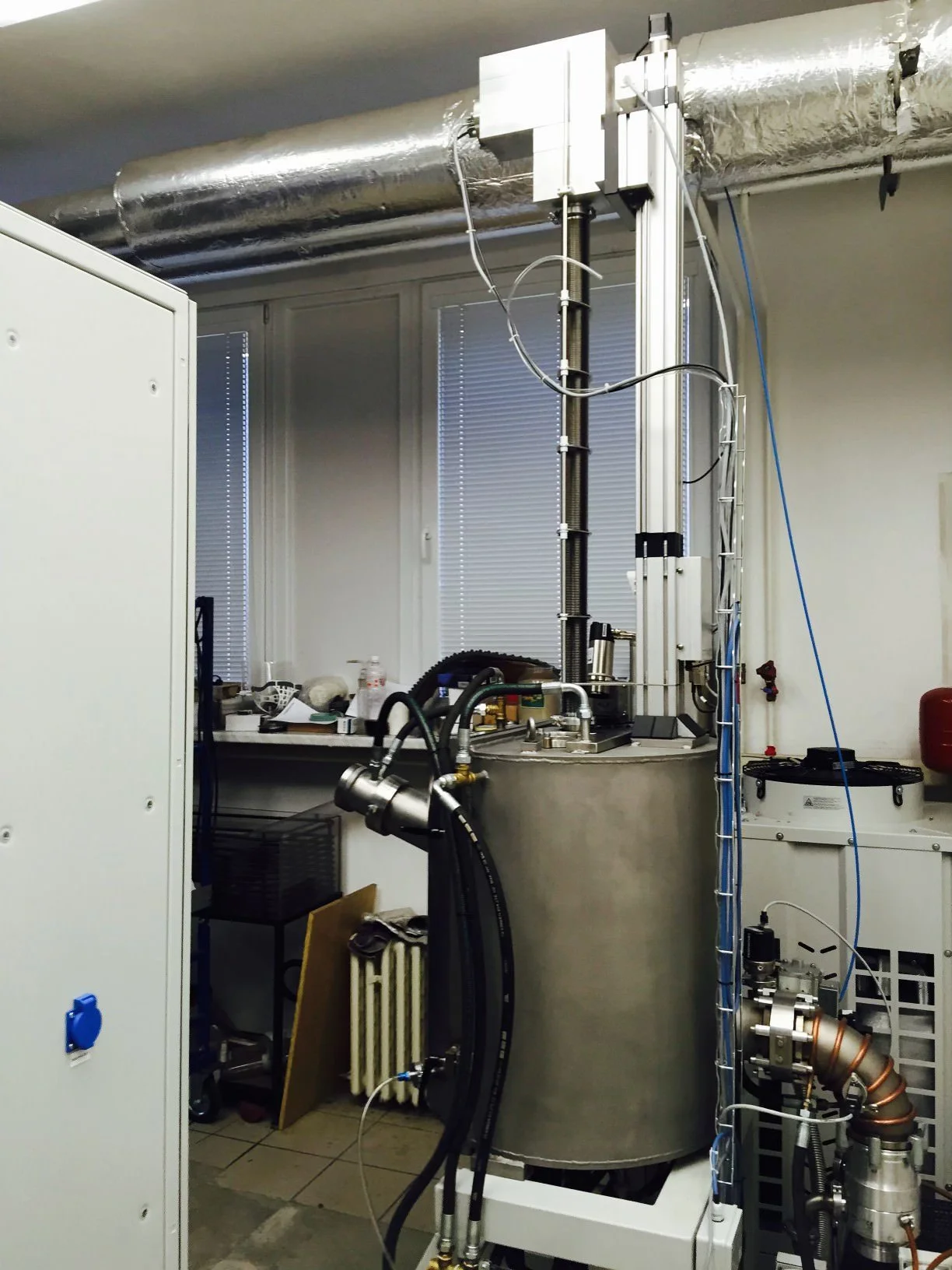
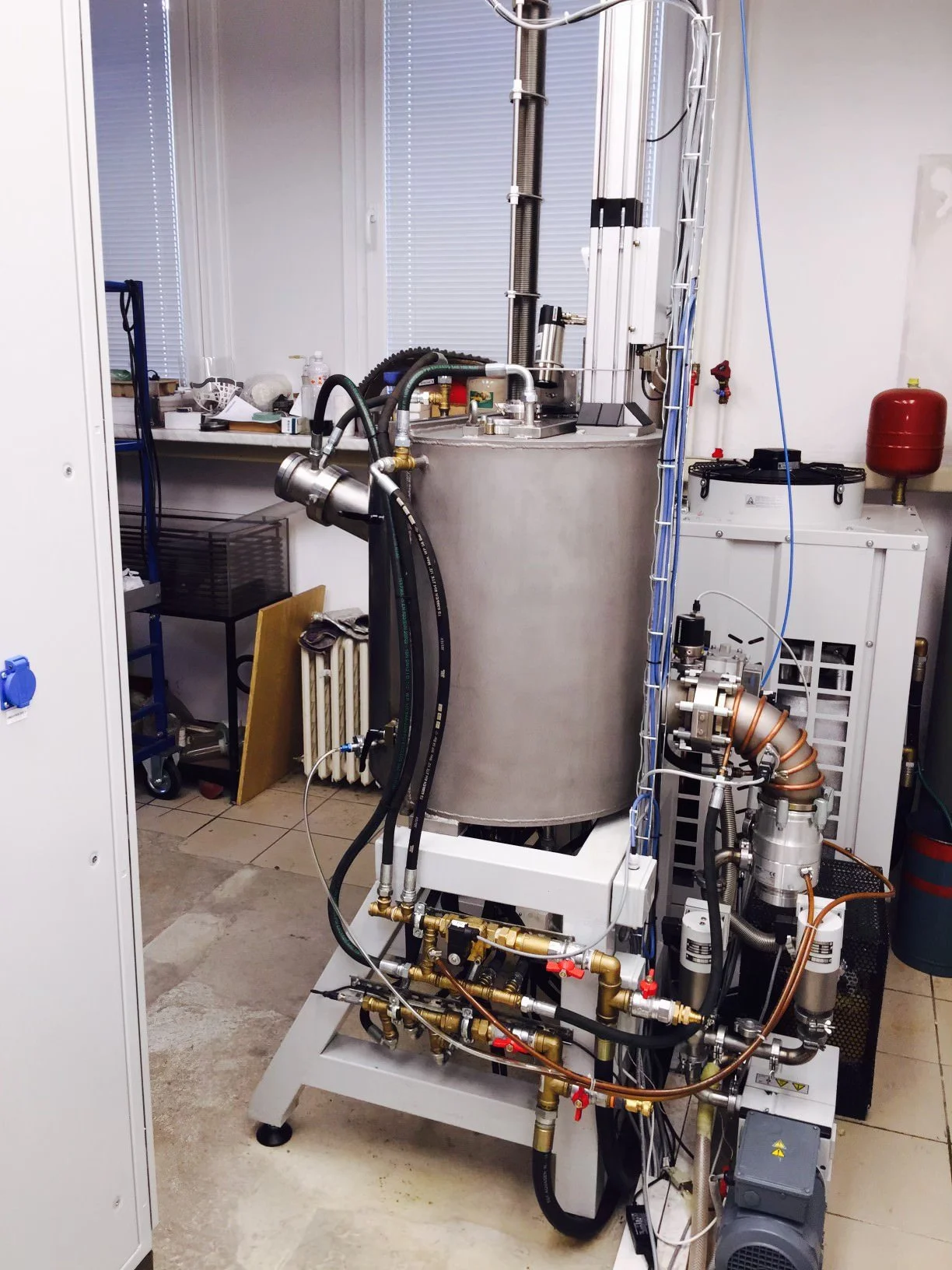
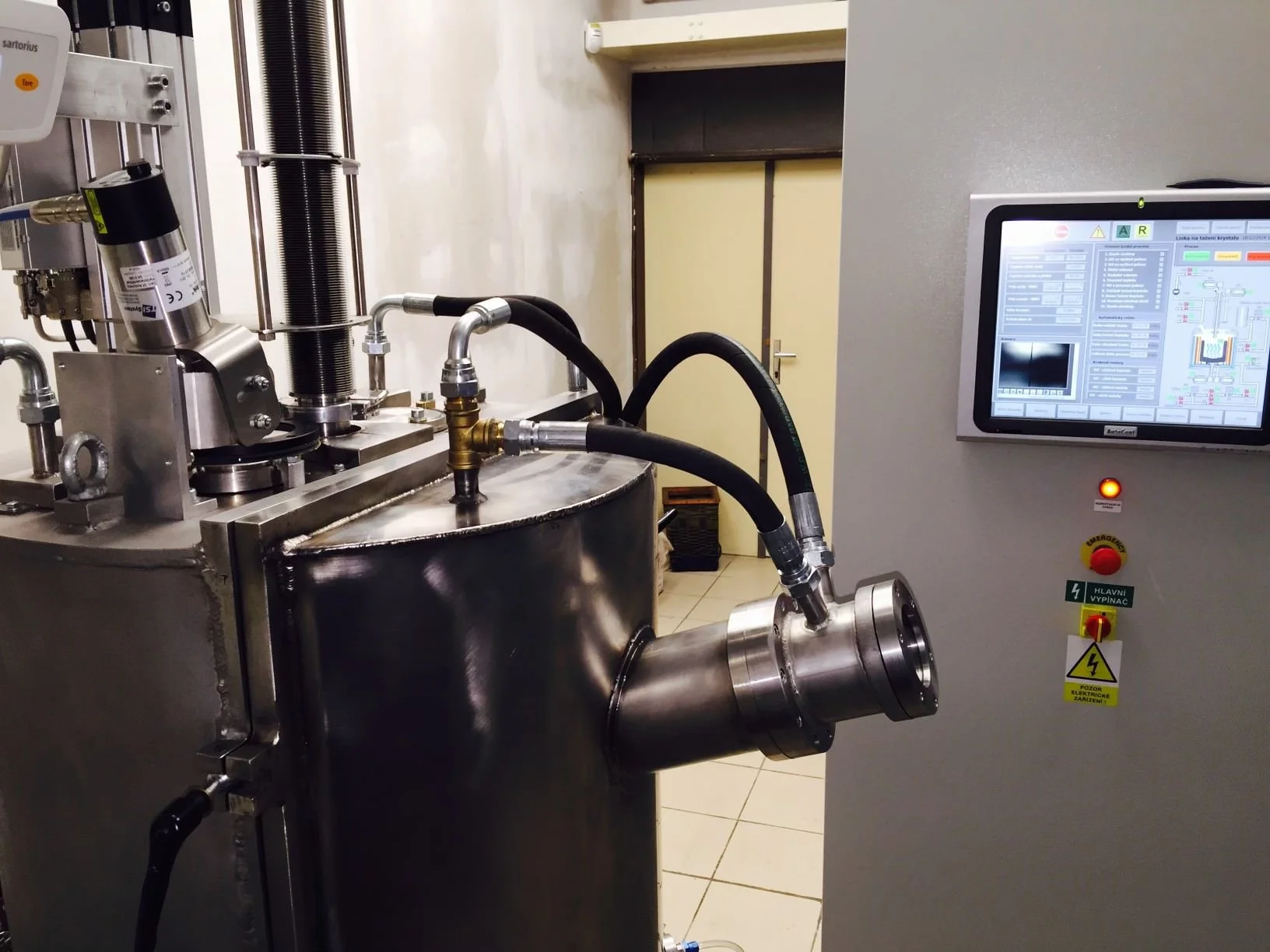
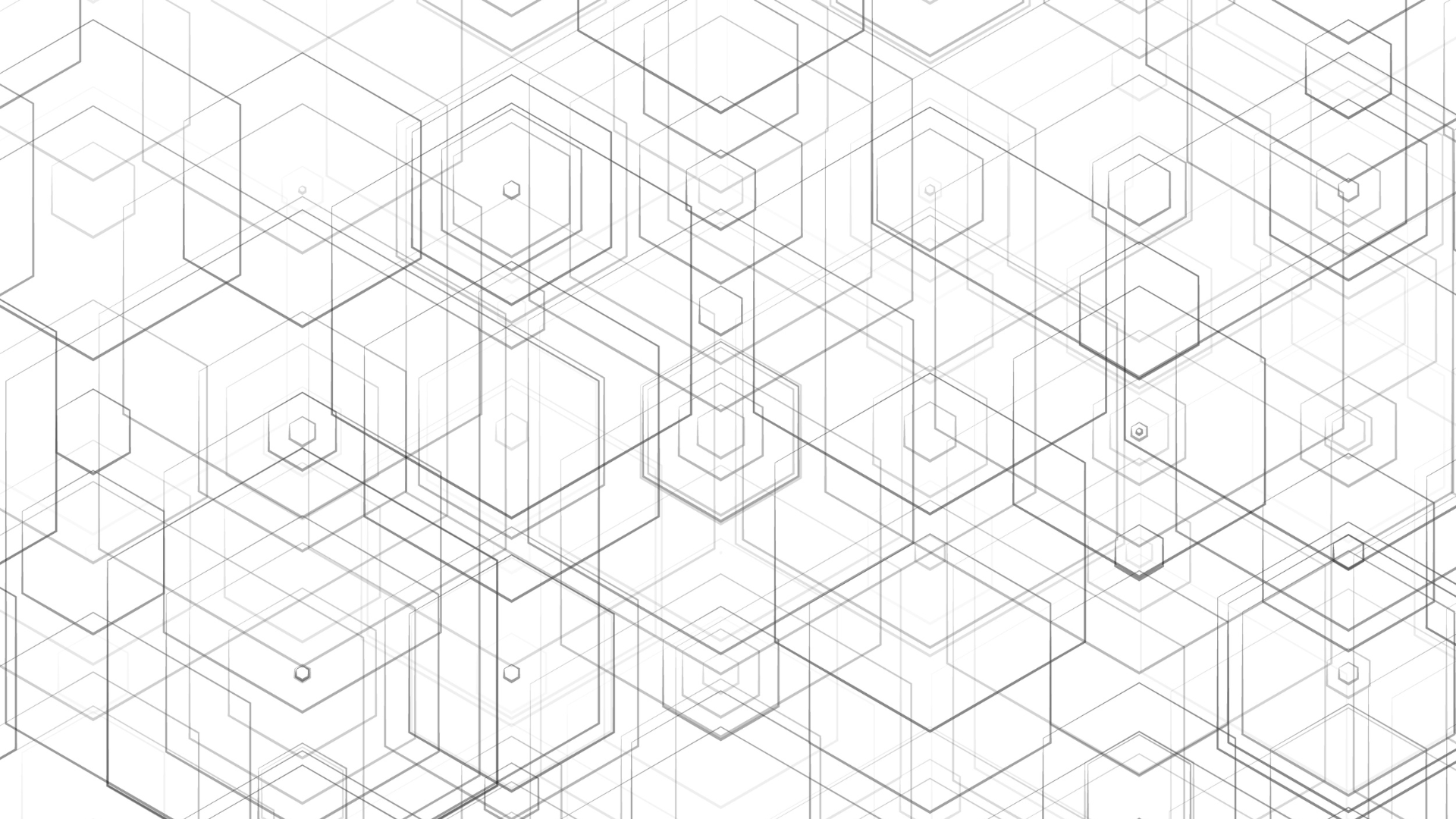